KOMATSU FrontRunner. Il sistema di trasporto autonomo AHS utilizzato da Boliden Aitik
Komatsu FrontRunner è il sistema di trasporto autonomo (AHS) che Boliden Aitik sta impiegando nella miniera satellite di Liikavaara. Un modo più sicuro, produttivo e preciso di gestire il flusso operativo nella più grande miniera di rame in Europa.
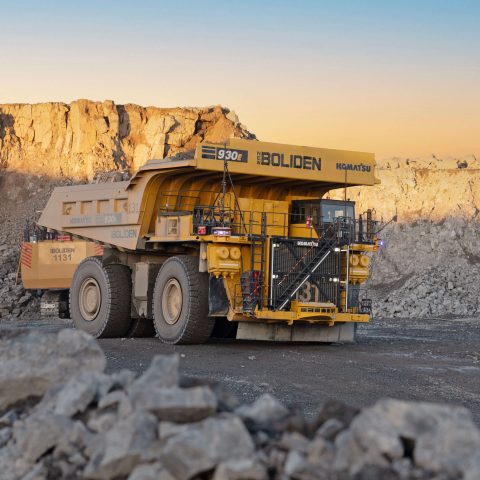
KOMATSU è stato tra i pionieri nello sviluppo di sistemi autonomi per la guida dei dumper. Non è quindi un caso se Boliden, colosso mondiale nel settore estrattivo, impiega il sistema di trasporto autonomo FrontRunner nella miniera di rame Aitik. Questa è oggi la più grande miniera europea di rame a cielo aperto. Un sito fondamentale da molti punti di vista.
Immaginiamo infatti che, con una rapida occhiata al proprio smartphone, si decida di incontrare degli amici in un locale preferito. Per evitare il traffico si sale su uno scooter elettrico e si sfreccia per le strade della città. Ovunque ci sono vivaci insegne di negozi, lampioni caldi e la luce fioca proveniente dagli schermi di innumerevoli passanti. Un mondo che, senza rendersene conto, ruota attorno al rame senza che ce ne rendiamo conto.
Dal momento in cui ci svegliamo, fino a quando ci addormentiamo, il rame è strettamente intrecciato nel tessuto della nostra vita. Si trova infatti nei fili che alimentano i dispositivi elettronici, nei tubi che trasportano l’acqua a casa nostra e nelle batterie che alimentano i veicoli elettrificati.
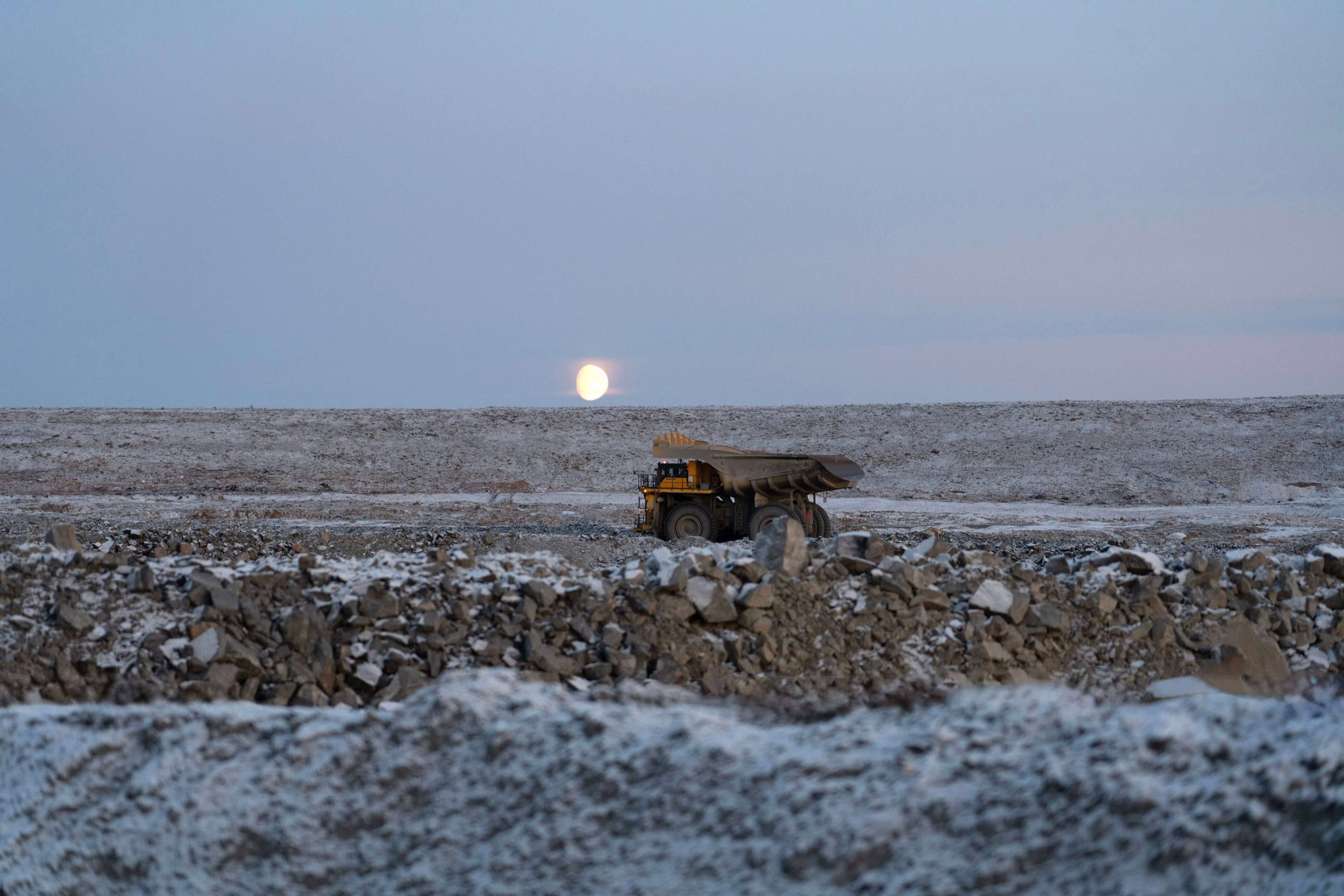
KOMATSU
Boliden Aitik si trova al Circolo Polare Artico in un ambiente ostile
Komatsu ed il rame di Boliden
Il rame non è quindi solo un elemento fondamentale della nostra vita ma è anche indispensabile per tutti i piani di transizione energetica. Ogni tipo di veicolo elettrico utilizza molto più rame rispetto ai veicoli tradizionali con motori a combustione interna. Secondo uno studio dell’International Copper Association, gli EV, compresi gli EV ibridi, rappresenteranno il 56% della domanda di rame da cablaggio nel 2032. Si tratta dunque di un aumento rispetto al 20% del 2022.
Soddisfare questa crescente domanda di rame in modo sostenibile non è semplice. Soprattutto in un periodo segnato da carenze di manodopera, instabilità geopolitica e cambiamenti climatici. Una possibile soluzione si trova sopra il Circolo Polare Artico, nel nord della Svezia. Parliamo proprio della miniera Aitik di Boliden Mineral AB.
Alcuni dati su Boliden Aitik
- Situata nella natura selvaggia della Svezia, Boliden Aitik è la più grande miniera di rame a cielo aperto d’Europa.
- Boliden estrae circa 40 milioni di tonnellate di minerale 24 ore su 24 da calcopirite che contiene rame, oro e argento.
- Ad ora la miniera a cielo aperto è lunga 3 km, larga 1,1 km e profonda 450 metri.
- Il lavoro ad Aitik viene svolto da alcuni dei macchinari più grandi, puliti e tecnologicamente più avanzati al mondo rendendola una delle miniere più sicure e produttive.
- Abbiamo quindi macchine gestite da un numero di donne quasi uguale a quello degli uomini rendendo Aitik una delle miniere con la maggiore parità di genere al mondo.
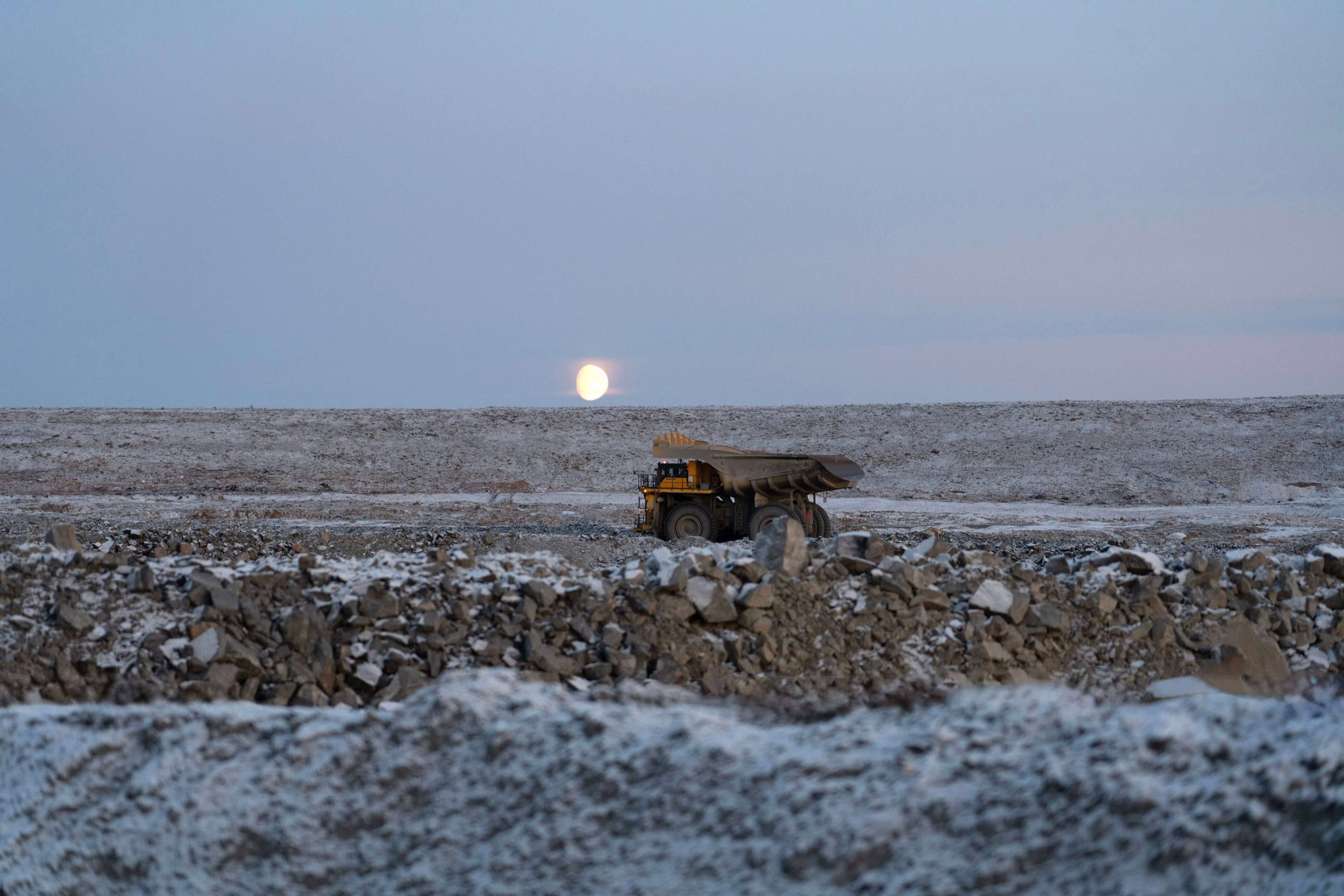
KOMATSU
Boliden Aitik si trova al Circolo Polare Artico in un ambiente ostile
La zona di lavoro autonomo
Aitik sta espandendo le sue operazioni con lo sviluppo della miniera satellite di Liikavaara. E’ situata a 3 km di distanza dal sito principale. Boliden sta implementando il sistema di trasporto autonomo FrontRunner (AHS) di Komatsu proprio nella miniera satellite di Liikavaara. Questo rende oggi Aitik la prima miniera in Europa e nell’ambiente artico ad utilizzare questo sistema di lavoro avanzato.
Tomas Eriksson-Ek, Direttore generale di Aitik, sottolinea “Il nostro primo obiettivo con il sistema AHS è l’aumento del livello di sicurezza. Vogliamo infatti eliminare rischi come scivolamenti o grandi massi che cadono accidentalmente causando potenziali lesioni agli operatori. Infatti ci saranno anche meno persone che lavoreranno fisicamente nell’area di produzione”.
Visto che i dumper Komatsu sono autonomi vi è anche minore incertezza nell’intero ciclo produttivo. Ciò comporta anche una maggiore produttività visto che le macchine possono essere utilizzate con turni di lavoro più intensi e produttivi.
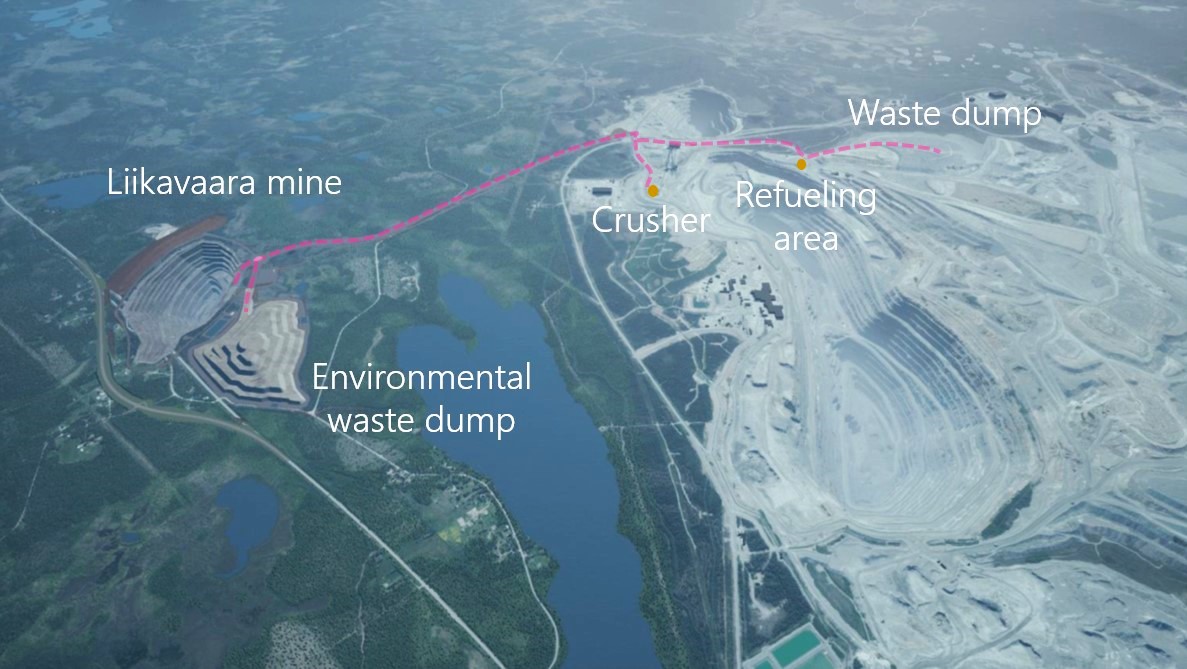
KOMATSU
Boliden Aitik ha mappato in modo attento la zona di lavoro autonomo
Komatsu FrontRunner
Il sistema FrontRunner (AHS) assicura anche che si utilizzino le macchine in modo ottimale. Questo migliorare anche la loro longevità riducendo i costi a lungo termine e ottimizzando i parametri di consumo. Un altro aspetto fondamentale è la precisione operativa. Infatti il sistema di Komatsu aiuta a posizionare i materiali nelle loro posizioni esatte. In questo modo si riduce il rischio di confusione minimizzando la necessità di correzione.
Rikard Mäki, responsabile dell’elettrificazione e dell’automazione presso Boliden, afferma “Nel lungo periodo prevediamo che il sistema AHS aumenterà ulteriormente la produttività. Questo ridurrà al minimo i tempi di fermo non programmati grazie ad una previsione più accurata della durata dei componenti. Infatti i dumper Komatsu sono costantemente guidati in base alle loro caratteristiche operative ottimali”.
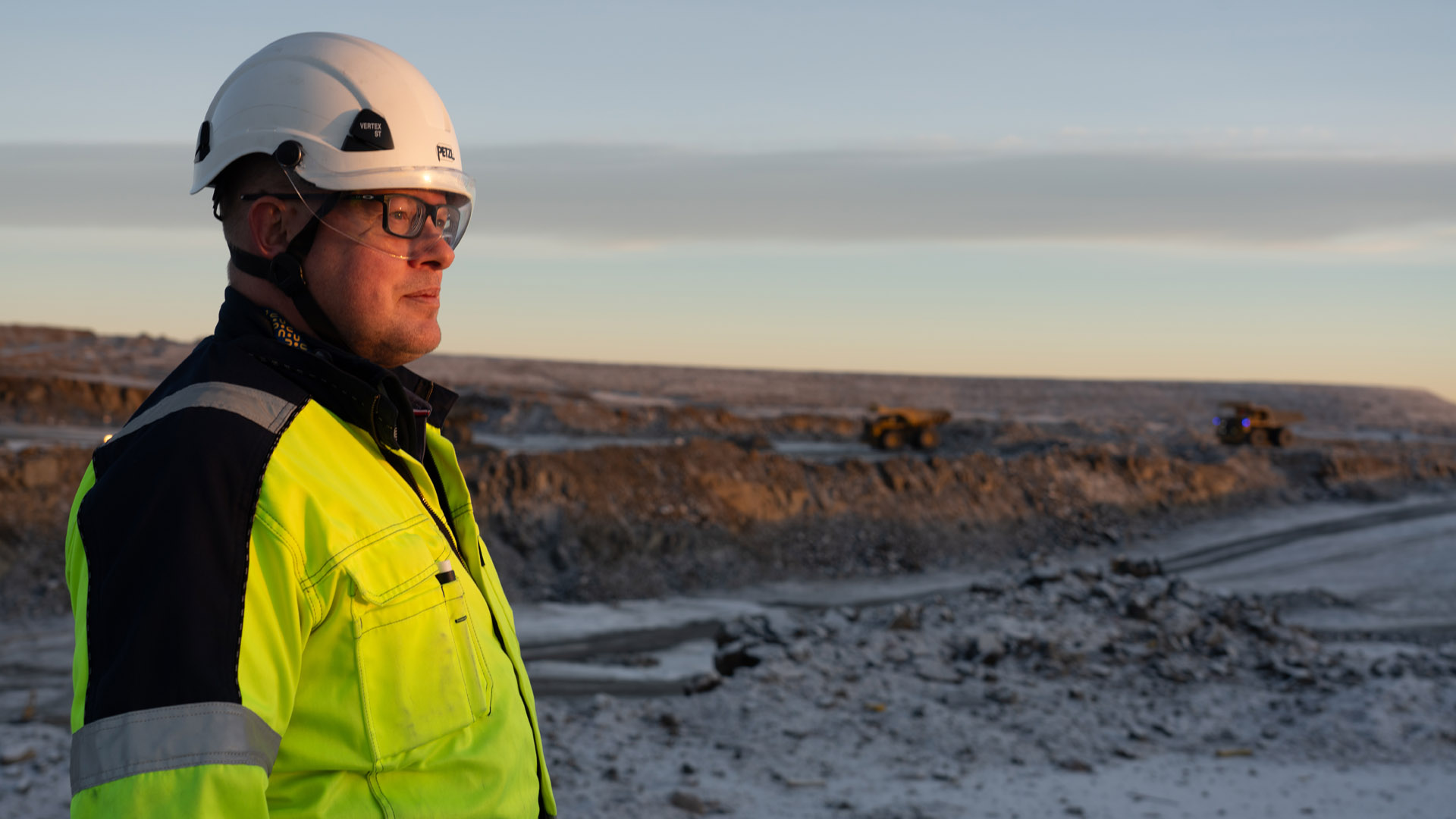
KOMATSU
Rikard Mäki è il responsabile dell’elettrificazione automazione di Boliden
L’automazione dei processi
Quando parliamo di sistemi AHS intendiamo molto più che togliere gli operatori dalle loro postazioni. Si tratta infatti di automatizzare e ottimizzare i processi operativi. L’implementazione del sistema autonomo di Komatsu parte con un piano di miniera efficace e produttivo. Infatti delinea gli obiettivi di produzione, le posizioni delle attrezzature e le richieste di lavorazione. Questi dati costituiscono la base per tutta l’automazione. Più efficace è il piano di miniera, più efficace risulta essere l’automazione.
Il passo successivo riguarda il sistema di gestione della flotta. In questo caso si parla del Komatsu DISPATCH. E’ un sistema che gestisce e analizza efficacemente la configurazione della miniera e tutti i requisiti di produzione. Queste informazioni sono trasmesse al sistema di supervisione AHS. E’ proprio qui che entra in gioco la tecnologia autonoma di Komatsu. Il sistema di supervisione (AHS) comunicherà quindi le assegnazioni alla navigazione dei dumper in modo rapido ed efficace.
Sottolinea ancora Rikard “L’implementazione di successo dell’automazione dipende dallo sviluppo organizzativo, dallo sviluppo della leadership e dall’empowerment della forza lavoro”.
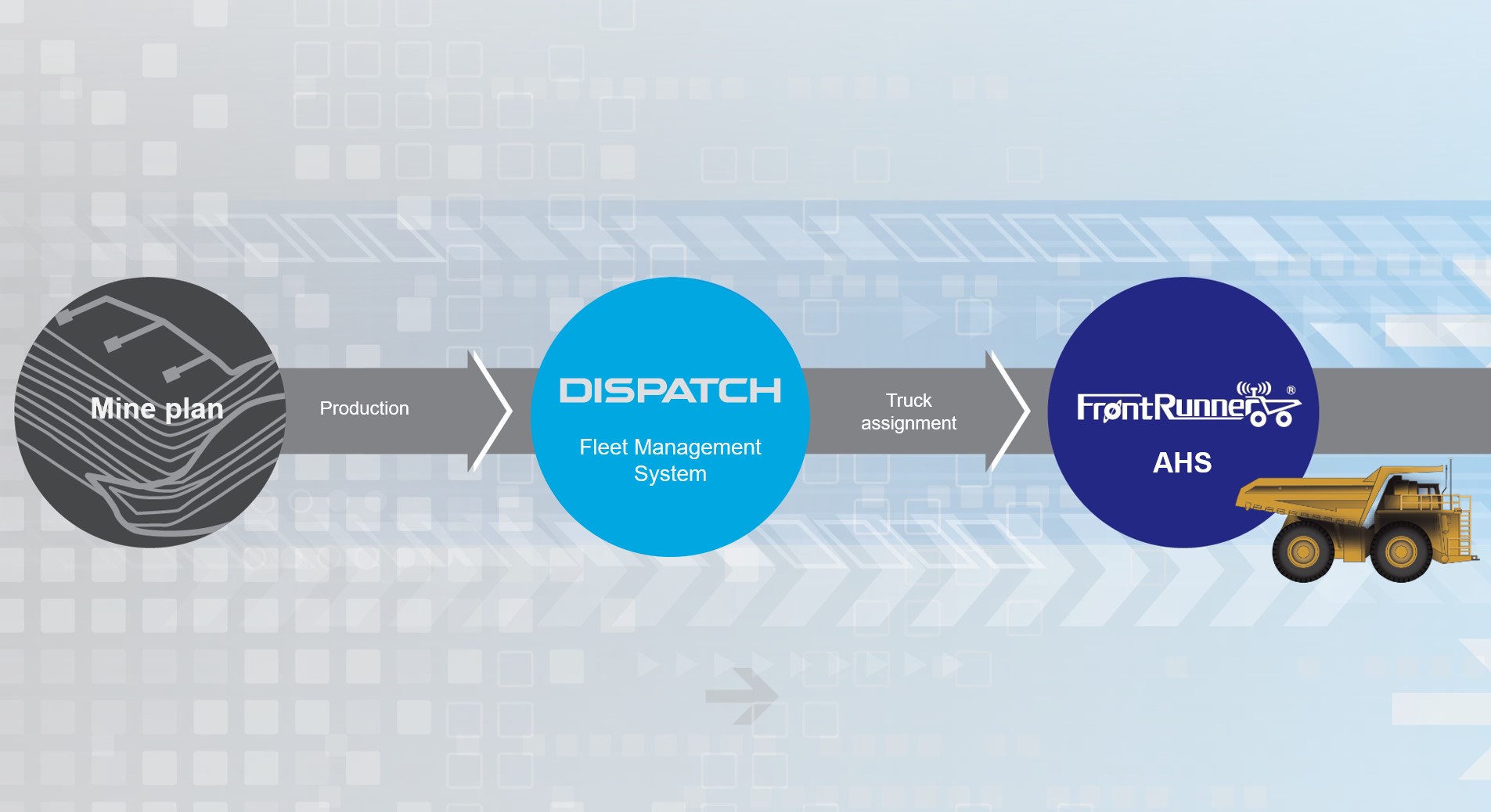
KOMATSU
FrontRunner ha permesso di automatizzare i processi operativi
Nuovi ruoli organizzativi
L’implementazione del sistema autonomo Komatsu in Boliden ha portato alla formazione di nuovi ruoli che richiedono competenze specialistiche. Si tratta di un processo di gestione del cambiamento che è guidato da un team di esperti di Komatsu e di Hesselberg Maskin AB, dealer locale del costruttore.
Uno di questi ruoli è il controller centrale. Una figura che gestisce il flusso dell’intera operazione dalla sala di controllo centrale assicurandosi che le cose funzionino in modo corretto. Grazie al software Komatsu FrontRunner si impostano i limiti di velocità, si controllano le condizioni stradali, i percorsi di scarico e tutte le altre variabili significativi per i dumper autonomi. Inoltre si interviene in caso di problemi. Questo avviene, ad esempio, in caso di guasto del dumper o della presenza di ostacoli lungo i percorsi. Infatti oggi gli istruttori di Hesselberg lavorano a stretto contatto con i controller centrali di Boliden nella sala di controllo assicurandosi che tutto funzioni in sicurezza.
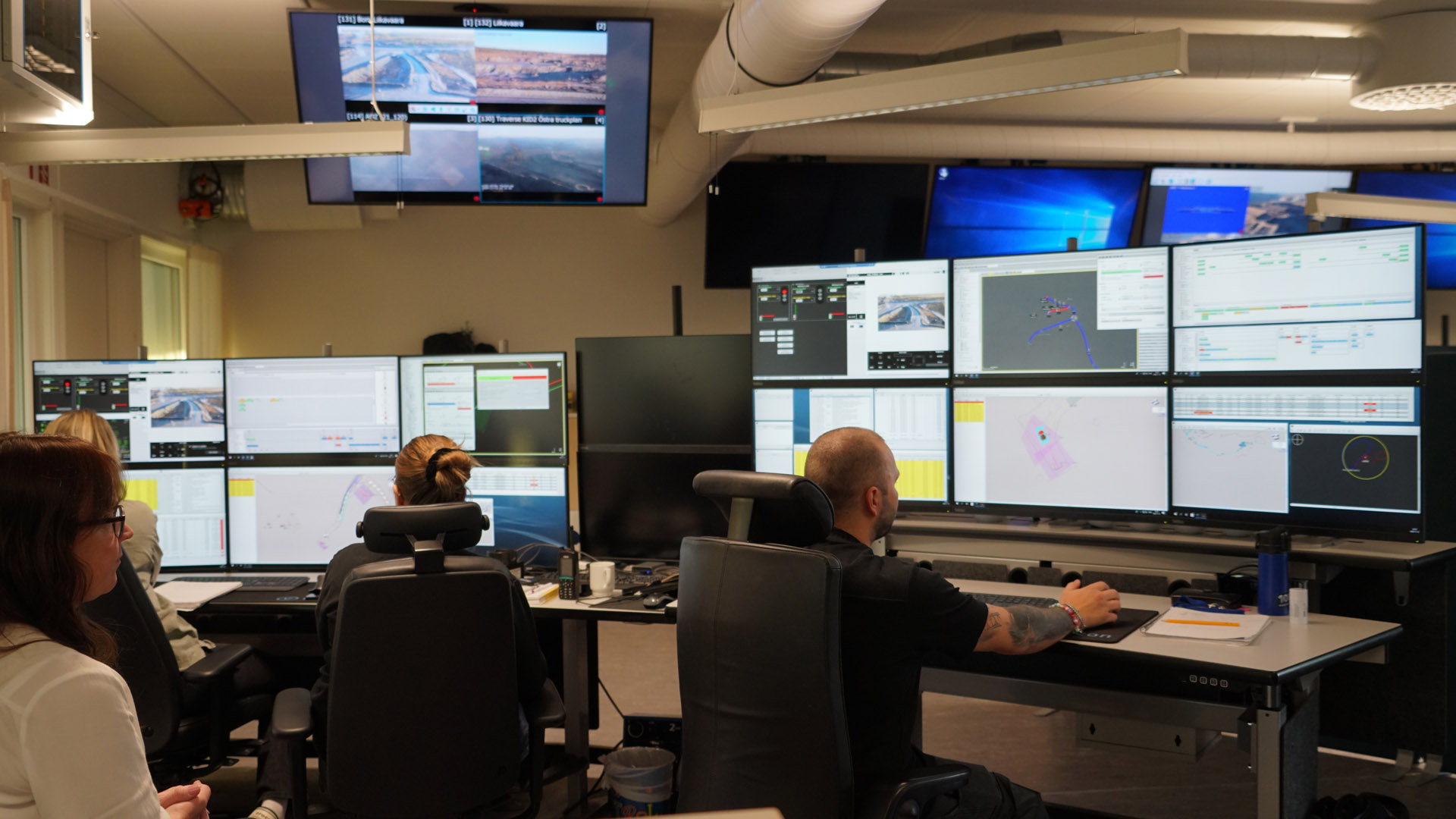
KOMATSU
La centrale di comando permette di avere migliori condizioni di lavoro
L’esperienza dei protagonisti e l’importanza della formazione
L’ex operatore Pontus Wallgren, ora controllore centrale, ci racconta come le sue condizioni di lavoro siano notevolmente migliorate “Prima trascorrevo innumerevoli ore su un dumper. Ma ora il mio lavoro è molto più ergonomico. Infatti posso interagire con le macchine da remoto in modo più comodo ed efficiente”.
Infatti il controllore centrale supervisiona l’operazione da una visuale a volo d’uccello. Invece la figura del controllore in campo funge da occhi e orecchie a terra. Se un dumper Komatsu si ferma a causa di un ostacolo può scoprire facilmente di cosa si tratta. Lo fa rimuovere e quindi riavvia il dumper dalla sua posizione comunicando alla sala di controllo centrale il nulla osta per continuare il lavoro.
Passare da lavorazioni manuali a quelle autonoma richiedono un solido programma di formazione per migliorare le competenze del personale. I formatori specializzati di Komatsu e Hesselberg sono infatti responsabili nel dotare il personale delle competenze necessarie. La formazione sono state svolte con simulatori.
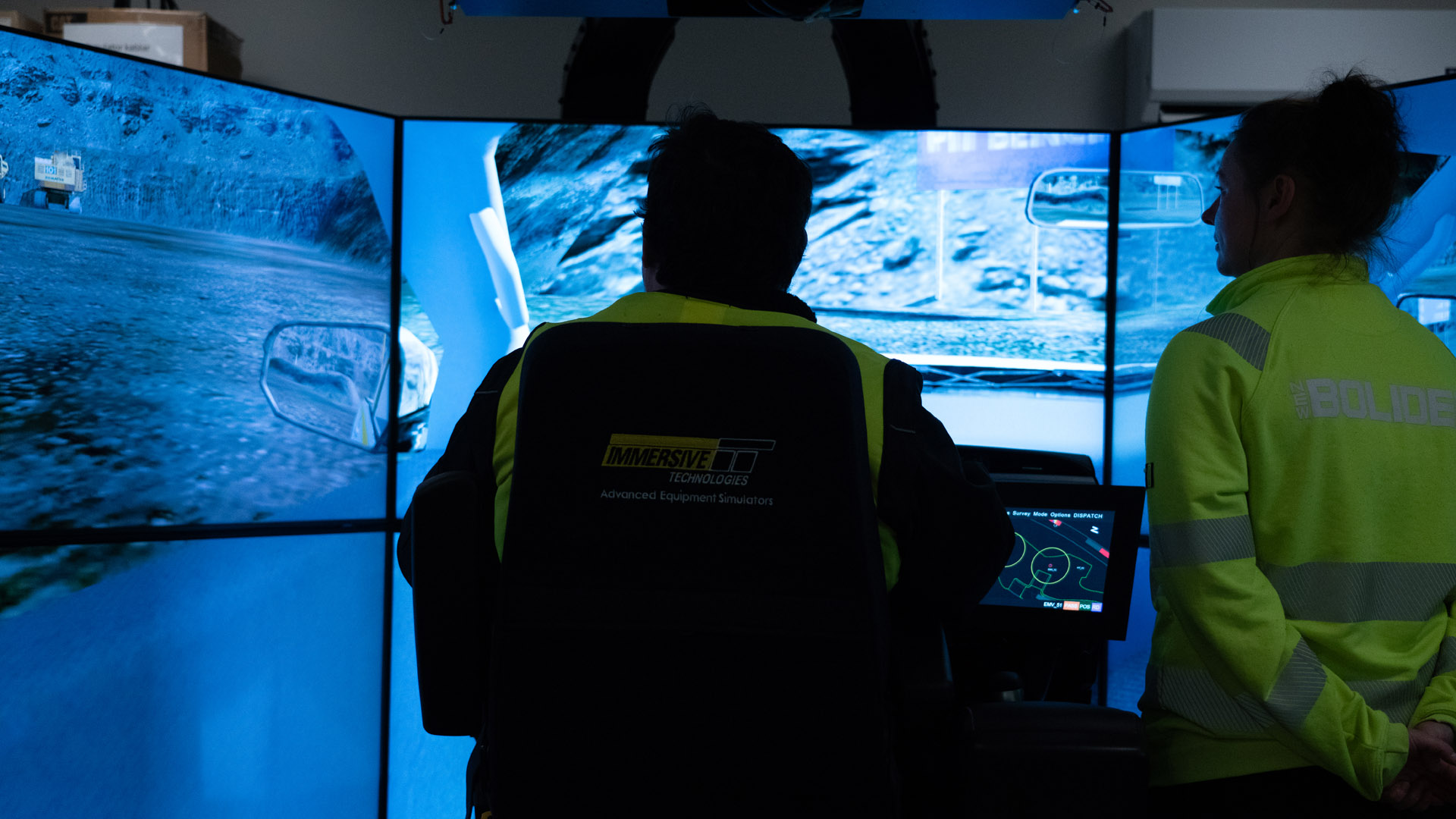
KOMATSU
La formazione degli operatori avviene tramite simulatori
Utilizzare i simulatori
Spiega Rikard Mäki “Abbiamo un team di formazione composta da 13-14 formatori che sono stati in loco per tutta la durata del progetto. Finora Aitik ha formato oltre 100 operatori per supportare la guida autonoma con i dumper Komatsu. Sono stati formati per ricoprire ruoli tradizionali come operatori di pale, dozer e grader e nuovi ruoli specificamente progettati per il sistema autonomo. La transizione verso il sistema AHS di Komatsu richiede uno sforzo collaborativo tra Boliden, Hesselberg e Komatsu stessa”.
E termina “Le tre aziende creano valore insieme liberando il pieno potenziale dell’automazione per garantire un sito minerario sicuro, pulito e produttivo. Oggi, tutta la produzione nella miniera di Liikavaara è gestita dal sistema Komatsu Frontrunner AHS 24 ore su 24, 7 giorni su 7. La flotta ha spostato circa 9 milioni di tonnellate di materiale. Di questi ben 5 milioni provengono da Liikavaara”.